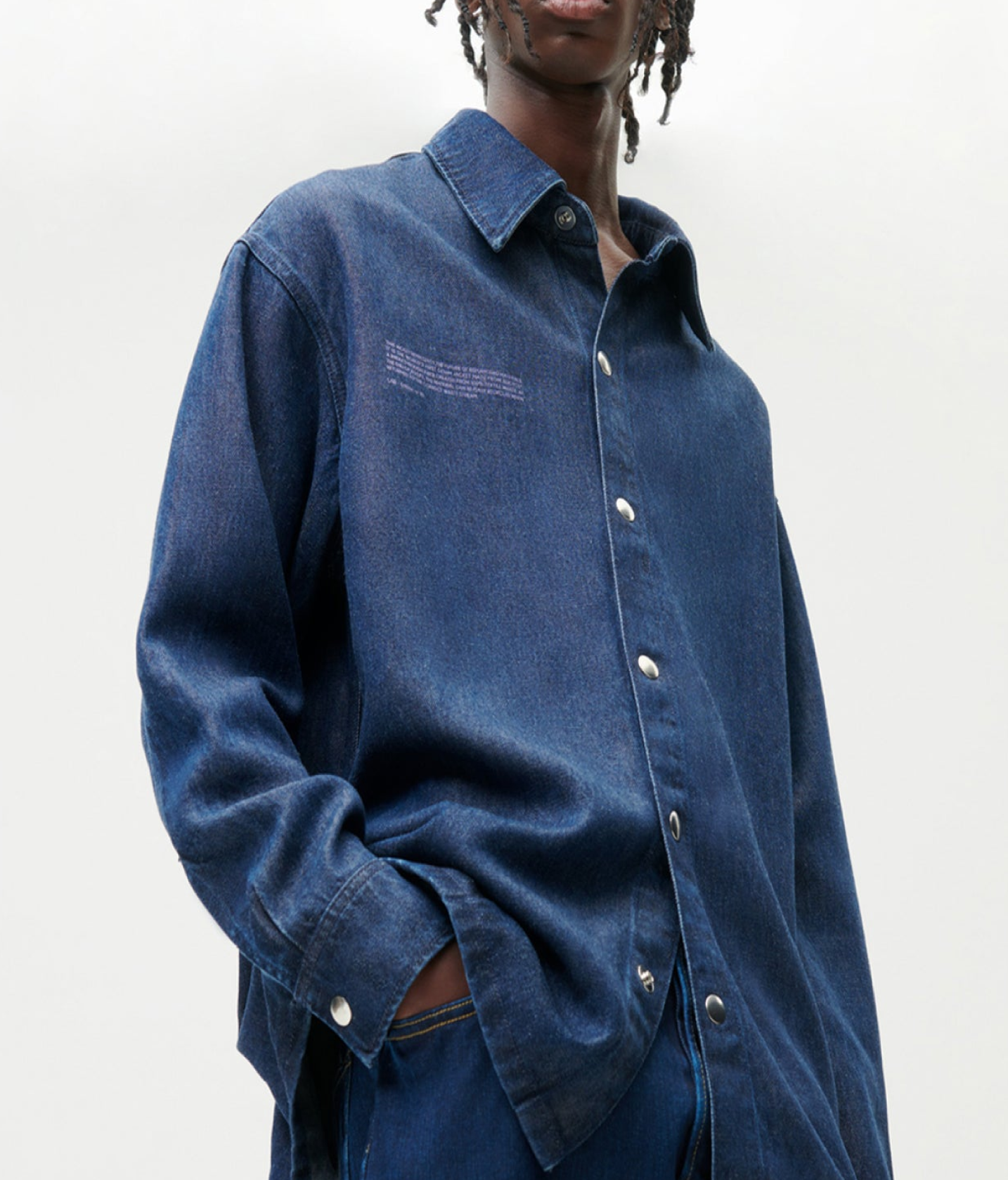
- |
- PRESS RELEASES
PANGAIA LAB
Materials Science Brand PANGAIA releases its latest innovation through PANGAIA Lab.
Our Nucycl® technology converts cotton waste into new fiber, which can be reformed again and again.
Discover MoreBy Brooke Roberts-Islam
It’s much-maligned by many fashion industry stakeholders that sustainability is a siloed challenge shuttled up and down the supply chain when only holistic and collaborative action can measure up to the global climate crisis. Consider the brilliant and exciting developments by many textile innovators, like recycled textile pulp in place of virgin tree pulp allowing the creation of circular fibers. Then consider that this pulp can be processed into environmentally safe and circular fibers like lyocell, or conversely, into rayon using harsh solvents that pollute wastewater and the environment and cannot be recycled.
System-wide solutions are needed to ensure total net benefits across textiles and products, rather than siloed benefits that may be canceled out by toxic dyeing or other processing methods further down the production line. One textile innovator has bitten off this entire textile waste to fiber problem and is integrating a suite of solutions from raw materials to final fiber and yarn: Evrnu.
Rather than tackling textile impacts from a specific material or technology point of view, Evrnu is developing a modular chemical and engineering platform that separates most textile waste types into fibers that can directly replace 90% of those in the current textile market, including cotton, man-made cellulosic fibers, nylon, and polyester.
But why this multi-fiber, multi-waste approach, which is in contrast to other innovators in the next-gen materials space who are focusing on specific challenges, like circular cotton-like fibers, or plant-based polyesters? Evrnu’s approach would seem to be more capital intensive, slower, and require very broad technical expertise. Furthermore, Evrnu is presenting a multi-pronged proposition for a market just beginning to dip its toe into the next-gen materials. I was curious to better understand why the company took on such a broad remit, so I interviewed co-founders Stacy Flynn (CEO) and Christopher Stanev, (President and CTO) in search of answers.
During a video interview, I learned that Evrnu’s mission was defined after Flynn spent a month visiting textile subcontractors in China, where toxic wastewater from mills was having a devastating and visible effect on local communities. That was in 2010. Evrnu was founded in 2014 by Flynn, a textile developer who previously worked at DuPont, Eddie Bauer, and Target; and Stanev, a textile chemistry and engineering expert with previous leadership positions at Nike, Gloria Jeans, and Target.
Evrnu’s purpose from the outset was to address the entire issue of textile waste and pollution. NuCycl, their chemical and engineering platform can “effectively recycle around 9 fiber types within textile waste” explained Stanev, accounting for most types of global textile waste. Outside of the scope are animal-based fibers, which account for less than 10% of the global fiber market. But how does NuCycl work?
The technology dissolves textile waste into its constituent ‘building blocks', whether they are cotton fiber, polyester, cellulose, or elastane. They are then separated, purified, and resynthesized into cellulose, polyester, and polyurethane (elastane) ready for respinning, or in the case of polyester, formation into pellets for extrusion into yarns or for other thermal molding purposes.
The chemistry used for dissolving the textiles depends on the material mix. For cellulose recovery, NMMO or ionic solutions are used. For PVC and polyurethane printed textiles, a solvent cocktail including organic (carbon-based) compounds is needed, which can be volatile and toxic. This solvent cocktail is still in development, according to Stanev, and is not part of their initial technology offering. The first technology ready for market is their textile waste to lyocell process, which has novel elements and will be licensed to cellulose pulp and fiber mills.
For their cellulose processing solution, the recycled textile pulp is processed into first-of-a-kind ultra-high-strength ‘r-lyocell’ fiber using a closed-loop lyocell process, with a twist. Stanev explained, “we are using the existing equipment but adding a specific reactor at the beginning [of the process] to change the morphology of the cellulose molecules so that they self-organize”. He likens this self-arrangement to that of spider silk. The process that occurs in the reactor to achieve this is liquid crystallinity, which causes the cellulose to rearrange into a stronger version of itself –but how, exactly, does this happen?
Cellulose is made up of carbon, hydrogen, and oxygen and Evrnu’s reactor causes the bonds holding these elements together to break and the hydrogen to be freed. The hydrogen then self-orientates before rebonding with the carbon and oxygen in an aligned structure, which is what delivers the final fiber’s superior tenacity (strength); NuCycl r-lyocell can withstand 6-8 grams of force per denier (a measure of yarn diameter), compared to conventional rayon at 2-3g and polyester at 3-5g.
Today, Evrnu launches their NuCycl r-lyocell in the “world’s first high-performance, recyclable lyocell material made entirely from cotton textile waste”. R-lyocell has been designed to replace and outperform virgin cellulosic and plastic-based materials, accounting for 90% of current textile fibers, and early indications show significant impact reductions while maintaining recyclability. Their first commercial product is a classic black t-shirt, made from 100% NuCycl r-lyocell, in partnership with designer Carlos Campos.
What are the limitations of r-lyocell, I asked Stanev? “It doesn’t repel water” he responded, explaining that hydrophobicity (water repellency) is a key characteristic of synthetic fibers like polyester, which r-lyocell is aiming to replace. But there are workarounds for this, and one potential technology that comes to my mind is MTIX’s MLSE platform, but that's a route of exploration and analysis for another chapter in this next-gen materials series.
So what are NuCycl’s r-Lyocell sustainability credentials? How do we know that this technology is net-positive in terms of all sustainability metrics–environmental and social?
Evrnu’s impact reduction estimates were calculated internally and for steering R&D decision-making–they have not been independently verified or peer-reviewed, and reflect a fiber still in development, not a scaled fiber in production. Therefore, despite having access to comparison data, I will share when the NuCycl pulp process is compared with Globalized Biorefinery Dissolving-Grade Wood Pulp and Globalized Kraft Paper-Grade Wood Pulp figures available on the Higg Index, it indicates a lower impact across all metrics. These metrics are Global Warming Potential (GWP, 100 years), Water usage, Fossil Fuels energy usage, Eutrophication, and Chemicals (human toxicity and water ecotoxicity).
In addition, 100% of textile waste inputs are diverted from landfills, reducing the environmental leaching of chemicals and microfibers. Inherent structural advantages of the fibers also allow for lower-impact dyeing and reduced chemical and energy use in the dyeing process, thereby showing improved environmental and social sustainability credentials.
To date, Evrnu has raised $31M, and their Series B funding round, led by Fullcycle, will close in April. The company is pre-revenue, but Flynn shared their forecast for production volumes and scaling: production of 17,000 metric tons (MT) of pulp in early 2023, and 2,000 MT of fiber later in 2023. These volumes are dwarfed by the millions of metric tonnes demanded by the global fiber market, but through licensing they aim to catalyze adoption and scale the technology, which Flynn explained integrates seamlessly into existing industry infrastructure.
Evrnu is currently in discussion with several licensees that are interested in adopting and scaling NuCycl technologies, starting at the 20 metric tonnes level and potentially ramping up to 100 metric tonnes for pulp and/or fiber.
After 8 years of R&D, today Evrnu has reached a milestone with its first commercial product launch, but I wonder what it will take to catalyze the next phase of next-gen material investment and adoption. Flynn reflects on the state of the industry and the magnitude of work to be done. “It will take 20 years to undo what we’ve done in the last 100 years,” she says of the toxic textile processes that have dominated. Today represents a major step on that journey, but what will it take to make these next 20 years count?
In her honest and open style, Flynn disclosed that the financial challenges and barriers to rapid scaling are “a classic tragedy of the commons,” regarding the industry’s reluctance to invest in sustainable innovations. “The key here is to get people to collaborate, but brands and retailers hesitate to put together offtake agreements, and financiers won’t finance [innovations] without offtake. Everyone’s sitting on the sidelines waiting to see what happens, but to not move is no longer an option”. Let that be the call to action–to move away from siloed shuffling of problems up and down the supply chain and instead collaborate for the benefit of net impact reduction from the raw material to the final product.
By clicking the button you're confirming that you agree with our terms and conditions.